Simulation der gepulsten elektrochemischen Metallbearbeitung (pECM) von dünnwandigen Bauteilen für den Triebwerksbau - SIMPECT
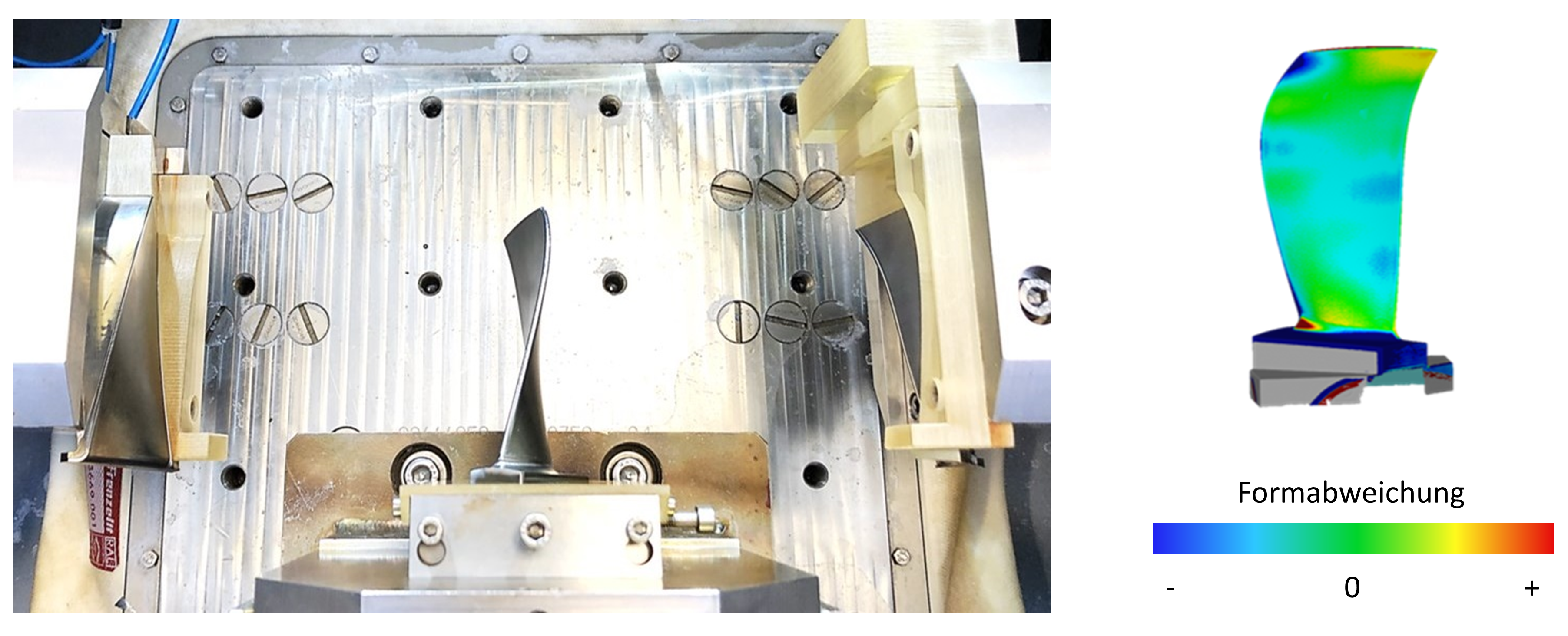
Abbildung: Triebwerksschaufel im Bearbeitungsraum einer pECM Maschine und Darstellung der Formabweichung nach der Bearbeitung
Mithilfe der präzisen elektrochemischen Metallbearbeitung (pECM) ist es möglich, höchste Anforderungen bezüglich der wiederholbaren Formgenauigkeit, den resultierenden Randzoneneigenschaften und der Oberflächengüte bei der Bearbeitung hochfester Metallwerkstoffe zu erfüllen, wie sie in der Turbomaschinenherstellung gefordert sind. Diese Vorteile ergeben sich bei durch die Art des Materialabtrags, welches auf dem Prinzip der Elektrolyse beruht. Die größte Herausforderung bleibt jedoch die Auslegung des Prozesses zur Fertigung neuer Bauteilgeometrien aufgrund der ungleichmäßigen Arbeitsspaltausbildung während des Prozesses, welche durch das komplexe Zusammenspiel mehrerer physikalischer Vorgänge vorliegt. Die etablierten heuristischen Auslegungsmethoden sind derzeit weder zeit- noch kosteneffizient, da durch diese „Versuch und Irrtum“ Methodiken kein nachhaltiges Prozessverständnis generiert wird. Detaillierte Kenntnisse über prozessbeeinflussende Aspekte sind allerdings essenziell, um effizientere Methoden, wie z.B. eine simulationsbasierte Werkzeugauslegung, zu entwickeln. Diese Defizite sollen mit diesem Forschungsvorhaben behoben werden, indem die pECM spezifischen Effekte sowohl numerisch als auch experimentell untersucht werden. Insbesondere soll erstmals eine grundlegende Untersuchung der Fluid-Struktur Interaktion (FSI) zwischen den oszillierenden Werkzeugelektroden und dünnwandigen Werkstücken erfolgen.
In der ersten Grundlagenphase wird eine generische Umgebung zur Simulation und Messung der strömungs- und strukturmechanischen Charakteristika des pECM Prozesses geschaffen. Der Arbeitsspalt des pECM Prozess, der ein typische Höhe von 50-250 µm besitzt, wird zur besseren messtechnischen Zugänglichkeit in einem experimentellen Aufbau unter Berücksichtigung von Ähnlichkeitskennzahlen hochskaliert. Die Bildung des Prozessgases aufgrund der elektrochemischen Reaktionen im Realprozess wird durch Einleitung von Gas durch poröse Wände in den wassergefüllten Kanal nachgebildet. Die FSI zwischen dem Werkstück und dem Elektrolyten des pECM Prozess, wird durch bewegliche Wände im Experiment modelliert. Parallel werden numerische Modelle für die mehrphasige Elektrolytströmung entwickelt. Diese werden mithilfe der experimentellen Messdaten validiert. Zur Modellierung der FSI, wird der numerische Löser der mehrphasigen Elektrolytströmung an einen strukturmechanischen Löser gekoppelt.
In der darauffolgenden Anwendungsphase werden die Erkenntnisse der Grundlagenphase für die gezielte Modellbildung zum Einfluss spülungsinduzierter Kräfte und der Ansammlung von Gasagglomeraten auf das elektrochemische Abtragverhalten einer realen Schaufelgeometrie eingesetzt. In der Optimierungsphase, d.h. der dritten Förderphase, soll schließlich ein Entscheidungsmodell auf Basis der gewonnenen Simulationsansätze entwickelt werden. Anhand des Modells wird für eine zu fertigende Geometrie und gegebene mechanische Eigenschaften eines Werkstoffs (Eingangsgrößen) unter Berücksichtigung einer geforderten Abtragrate sowie geometrischen Toleranz (Zielgrößen) der zugehörige Prozessparametersatz ermittelt. Basis dieses Entscheidungsmodells ist die Untersuchung der Zweiphasenströmung im Elektrolytkanal während des elektrochemischen Abtragprozesses und die daraus resultierenden mechanischen Kräfte. Hiermit sollen spülungsinduzierte Schwingungen und Einflüsse von lokalen Gasagglomeraten derart minimiert bzw. begrenzt werden, dass die Abbildegenauigkeit erhöht und eine toleranzsichere und effiziente Fertigung ermöglicht wird.
Antragsteller:
Projektbearbeiter:
Univ.-Prof. Dr.-Ing. Wolfgang Schröder
Lehrstuhl für Strömungslehre und Aerodynamisches Institut
RWTH Aachen
Telefon: +49 241 80 95410
E-Mail: office@aia.rwth-aachen.de
Daniel Lauwers, M.Sc.
Lehrstuhl für Strömungslehre und Aerodynamisches Institut
RWTH Aachen
Telefon: +49 241 80 90404
E-Mail: d.lauwers@aia.rwth-aachen.de
Dr.-Ing. Andreas Klink
Werkzeugmaschinenlabor WZL
RWTH Aachen
Telefon: +49 241 80 28242
E-Mail: a.klink@wzl.rwth-aachen.de
Elio Tchoupe, M.Sc.
Werkzeugmaschinenlabor WZL
RWTH Aachen
Telefon: +49 241 80 28037